Jaw crushers produce very little fines and are therefore ideal for primary crushing. The 4 to 1 reduction ratio of a jaw crusher makes it suitable for low volume applications. Nevertheless, a jaw crusher cannot produce high volumes of low-quality products. That is why it is used as a primary crusher, producing the least amount of fines possible and maximising the usability of the end product.
Grizzly-King Heavy Duty Jaw Crusher
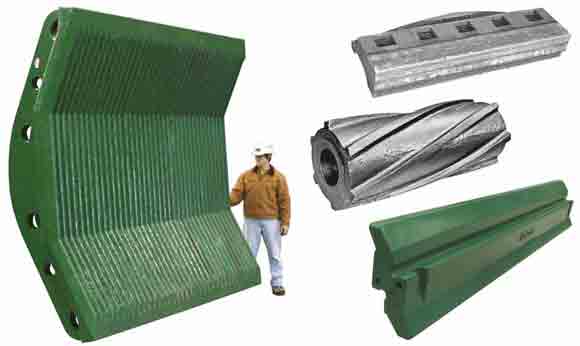
The Grizzly-King Heavy Duty jaw crusher is one of the most powerful pieces of industrial crushing equipment available today. Its massive frame construction and heavy steel sections ensure the durability and performance of this heavy-duty machine. The jaws of the Grizzly-King Heavy Duty crusher have a longer stroke and narrower nip angle than their counterparts, resulting in increased positive bite and reduced pinched-out rocks. It also features an eccentric jaw motion to force materials through the crushing chamber and increase production. The result is an impressive 950-ton/hr processing capacity.
The Grizzly-King Heavy Duty jaw crusher is also equipped with a vibrating grizzly feeder that has AR steel liners. It comes with a front discharge conveyor and has guards for all drive mechanisms. The unit also comes with a tool box and stoplights for safety.
Jaw crusher lubrication system has an outstanding performance
In order to ensure the long-term performance of a jaw crusher, its lubrication system must be well maintained. This includes checking oil in the return tube for dirt and metal dust, ensuring that the jaw plate is not worn and tightening all transmission parts. This type of sundries will accelerate wear and shorten the equipment’s lifespan. You should also clean the lubricating oil filter with gasoline, and it should be allowed to dry completely before re-using the crusher, Check out this site.
Lubrication is critical in jaw crushers because of the heavy load placed on it. Therefore, jaw crusher lubrication systems are carefully designed to ensure positive lubrication to the points of highest pressure. motor-driven pump forces lubricant through a series of cylinders, forcing it through the jaw crusher’s high-pressure lubricator. This then disburses the lubricant to the bearings in a controlled manner.
Jaw crusher is a primary crusher
The size of the finished product depends on the gap between the jaws at the discharge outlet. The crushing ratio of a jaw crusher is typically six to eight. In other words, the feed material is reduced by about six or eight times before it reaches the discharge outlet. Typically, a jaw crusher produces a cubical product of up to 20mm in size.
The disadvantage of the jaw crusher is that it is not suited to a wide variety of materials. Its 4:1 reduction ratio means that it cannot handle large volumes of material of low quality. However, the jaw crusher’s reduced size results in minimum fines, thereby maximising the usability of the end product.
Jaw crusher is more rugged than gyratory crusher
The differences between a jaw crusher and gyratory crusher are largely based on the way they crush materials. A jaw crusher uses a compression principle to crush materials, while a gyratory crusher uses a discontinuous impact method to crush materials. Both have the ability to reduce large amounts of material, but a gyratory crusher has a longer maintenance interval.
Jaw crushers are better suited to primary crushing applications. They can take on tough, abrasive materials and offer a better reduction ratio than gyratory crushers. The disadvantages of gyratory crushers include higher capital and operating costs, and the requirement for a large housing structure. However, if you only need a small amount of raw material for primary crushing, a jaw crusher is the perfect choice.
Jaw crusher is used in industrial laboratories
Jaw crusher is a common laboratory instrument used for the pre-crushing of hard and brittle materials. The jaw crusher has two crushing jaws, one fixed and one movable, which follow an elliptical path. The jaws crush the material by applying pressure and the crushed particles fall into a collection receptacle once they reach a specified size.
Summary:
Jaw crushers can be used to crush various materials, ranging from 40 mm to 350 mm. They are used in many different fields, including materials research, environmental analysis, and construction materials.